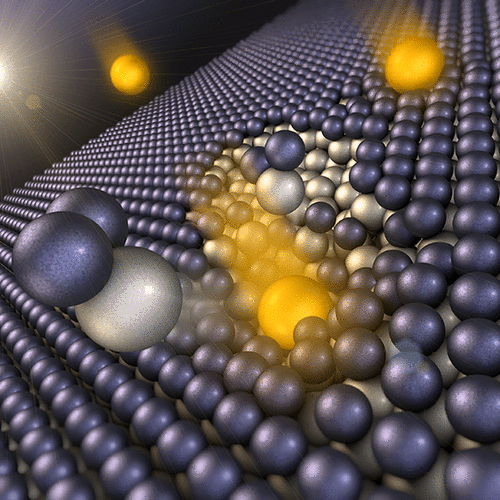
Atomic Layer Etching
Atomic Layer Etching (ALE)

Etching is a key step in semiconductor process. Up to date, most of etching process had been conducted by using plasma, generating highly energetic radicals in order to make a volatile etch species by the reaction with materials. However, damage induced by the energetic species cannot be negligible anymore as device scales down to sub-10 nm. Thus, a need of a new etching process which doesn’t use plasma or high energy radicals becomes more and more important.
The advantages of ALD such as excellent conformality and precise thickness control at the atomic scale over the conventional thin film deposition methods are its direct attractiveness for the nanoscale fabrication in a three-dimensional (3D) structure. Additionally, the cyclic exposure of the precursor and reactant in ALD reactions is another factor to enhance the atomic precision properties of thin films. For example, doping in films at the desired depth position is feasible by only adding dopant chemical exposure to normal ALD cycles without using expensive and complex tools, such as ion implantation. Additionally, metal alloys can be easily fabricated by combining two metal ALD processes. Considering that the amount of each metal can be controlled by the number of ALD cycle, a precise compositional control of alloy metals is also feasible, one of the advantages for the catalytic property maximization.

Thermal atomic layer etching (ALE), the opposite reaction of atomic layer deposition (ALD), is considered as a promising etch technique that can overcome the damage. ALE is based on sequential, self-limiting surface reaction, same with ALD. As shown in the figure above, a precursor (or reactant A) modifies surface of a material, then a following precursor reacts with the modified layer, making volatile species. In this manner, the ALE ensures 1) atomic thickness controllability, 2) large area uniformity, and 3) isotropic etching. In particular, the traditional etching techniques such as reactive ion etching (RIE) have anisotropic etching due to the directionality of energetic ion species, whereas thermal ALE etches isotropically, it can be used for uniform etching to fabricate 3-d structured devices such as nanowire field effect transistor (NW FET).